


In setting up a mechanically operated shaper, the length of cut (in inches) is known, and the cutting speed (in feet per minute) is selected according to the kind of metal being cut. However, if the cutting speed chosen is somewhat on the slow side, the average speed may be used, and computations are greatly simplified.Īlthough the ratio varies somewhat, several shapers have a linkage using 220 degrees of the cycle for the cutting stroke and 140 degrees for the return stroke. The maximum is at the center of the stroke. The RPM of the bull gear becomes the strokes per minute (sometimes abbreviated SPM) of the shaper.Ĭutting Speed: The cutting speed of the tool across the work will vary during the stroke as shown by the velocity diagram. The bull gear is driven by a pinion which is connected to the motor shaft through a gear box with four, eight or more speeds available. The less expensive shaper, the one most often purchased, uses a mechanical drive. Figures below show diagrams of both shaper drive mechanisms. Shapers are available with either mechanical or hydraulic drive mechanisms. The maximum vertical height available is about 12" to 15". Most shapers have a width capacity equal to or greater than the length of the stroke.
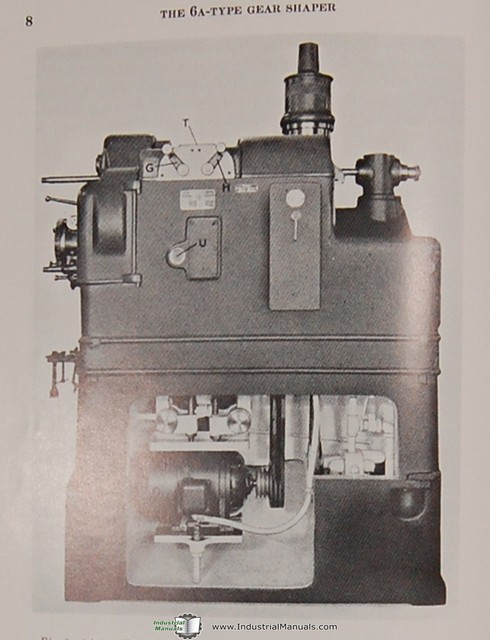
Shaper Width: The maximum width which can be cut depends on the available movement of the table. These shapers use from 2- to 5-hp motors to drive the head and the automatic feed. Horizontal shapers are most often made with strokes from 16- to 24" long, though some smaller and larger sizes are available. Shaper Size: The size of a shaper is the maximum length of stroke which it can take. Work that cannot be held in the vise (due to size or shape) is clamped directly to the shaper table in much the same way as parts are secured on milling machine tables. The vise may also have a swivel base so that cuts may be made at an angle. The vise is specially designed for use in shapers and has long ways which allow the jaws to open up to 14" or more, therefore quite large workpieces can be held. Workholding: Workholding is frequently done in a vise. just as in the lathe, but in a vertical plane. These cutters are fastened into the toolholder. The cutter is sharpened with rake and clearance angles similar to lathe tools though the angles are smaller because the work surface is usually flat. Toolholders: Toolholders are the same as the ones used on at engine lathe, though often larger in size. The mechanism for moving the ram and table is housed inside the column. Final depth can be set by the hand crank on the tool head.Ĭolumn: The column supports the ram and the rails for the saddle. Saddle: The saddle moves up and down (Y axis), usually manually, to set the rough position of the depth of cut. Then, either by hand or more often automatically, the table is moved sideways to feed the work under the cutter at the end or beginning of each stroke. Table: The table is moved left and right, usually by hand, to position the work under the cutter when setting up. Often this clapper box is automatically raised by mechanical, air, or hydraulic action. The clapper box is hinged so that the cutting too] will not dig in. The block holding the tool post can be rotated a few degrees so that the cutter may be properly positioned in the cut.Ĭlapper Box: The clapper box is needed because the cutter drags over the work on the return stroke. This has a tool post very similar to that used on the engine lathe. Attached to the toolhead is the toolholding section. The toolhead can also be moved up or down by its hand crank for precise depth adjustments. Toolhead: The toolhead is fastened to the ram on a circular plate so that it can be rotated for making angular cuts. The starting point and the length of the stroke can be adjusted. Ram: The ram slides back and forth in dovetail or square ways to transmit power to the cutter. The horizontal shaper is the most common type, and its principal components are shown below, and described as follows: Tooling is simple, and shapers do not always require operator attention while cutting. It is used fairly often in the toolroom or for machining one or two pieces for prototype work. The shaper is a relatively simple machine. However, the return stroke is made at up to twice speed of the cutting stroke. The planer handles work weighing up to several tons.īoth the shaper and planer usually cut only in one direction, so that the return stroke is lost time. The cutting stroke of the planer is achieved by moving the work past a stationary tool bit. Moving the tool bit attached to the ram makes the cutting stroke of the shaper. The planer handles work weighing up to several tons. The shaper handles relatively small work. Both the shaper and the planer are single-point tools that cut only in straight lines.
